山西焦煤集团有限责任公司是本专业在2017年新开辟的生产/毕业实习基地之一,主要目的是专业设备及其成套装置和过程控制,化工产品生产、煤气生产、发电等,包括焦化一厂和焦化二厂。学生在该厂主要了解化工产品—工艺和设备,包括气体、固体产品。
山西焦煤集团公司西山煤气化公司始建于1991年,公司位于古交市马兰镇七佛沟,是古交市城市煤气的气源厂。目前我公司拥有中压管网80多km,低压管网200km,煤气用户3万余户。按照古交市“十一五”期间城市发展总体规划,煤气的城市居民用户、商业用户、工业用户都将有较大增长;预计到2015年,日煤气需求将增长到30万m3。而西山煤气化公司原66-4型2*25孔焦炉日供煤气仅4万m3,已不能满足城市需要。为了从根本上解决古交城市气源长期稳定供应问题,按照省政府批准的古交市(2003-2020)城市建设发展规划,我公司焦化一厂承建了气源替代项目TJL5550D 1*65孔,60万吨焦化技术改造工程。
1. 焦化一厂焦炉工艺:
TJL5550D型为宽炭化室、双联火道、废气循环、下喷式捣固焦炉,炭化室长度15米98。,有效长度15米14,全高5.5米,平均宽度500mm,锥度10mm,32个立火道,年消耗干煤量843851吨,年产干全焦达64万多吨。这个型号的焦炉是在总结了多年焦炉设计及生产经验的基础上研发的新炉型,特点如下:
(1)炉炭化室平均宽度为500mm,属于宽炭化室焦炉,具有可改善焦炭质量和增大焦炭块度的优点。另外,产量相同时,还具有减少出焦次数,减少机械磨损,降低劳动强度,改善操作环境,减少无组织排放的优点;
(2)在炉底铺设新型材料漂珠砖,以减少炉底散热,从而大大地降低地下室温度,改善炉底操作环境;
(3)小烟道采用扩散型蓖子砖,砖的上下表面孔径大小恰好相反,对于一个小烟道,下表面从外到里孔径由小到大,上表面由外到里孔径由大到小,由此来克服小烟道内变量气体所产生的内外压力差,达到调节小烟道内变量气体流量的目的,从而使蓄热室内气体分布均匀,实现焦炉长向加热均匀性;
(4)蓄热室主墙是用带有两条沟舌的异型砖相互咬合砌筑的,蓄热室单墙为单沟舌结构,用异型砖相互咬合砌筑,保证了炉墙的整体性和严密性。
(5)蓄热室内装有薄壁大蓄热面积的12孔格子砖,可有效降低废气离开蓄热室时的温度吗,同时还可以预热外来的空气,充分利用了余热,节省了热源的消耗。
(6)为了提高边火道温度,增加蓄热室封墙的严密性,减少热损失,降低地下室及烟道走廊的温度,在蓄热室封墙及斜道炉头部位,采用隔热效果好且在高温下不易龟裂的新型保温隔热材料;
(7)燃烧室采用废气循环和高低灯头的结构,保证了焦炉高向加热的均匀性;
(8)加热水平为800mm,可使焦饼上下同时成熟,并可减少炉顶空间的石墨生成量;
(9)炉顶除尘孔和上升管孔砌体采用带有沟舌的异型砖砌筑,保证了它的整体性,使炉顶结构更加严密,减少了荒煤气的窜漏,从而有效地防止了炉顶横拉条的烧损;
(10)在加宽炭化室的情况下,为保证焦炉的结构强度,采用加大炉柱的护炉能力,炉柱由常用的工字钢改为H型钢。
(11)在总结生产经验的基础上,对立火道底部的斜道口断面面积和调节砖进行了计算和设计,通过合理排列调节砖,使燃烧室各火道的气量分配合理,横排温度分布均匀,从而保证焦炭质量和焦炉热效率。
(12)炉顶面焦炉中心至机、焦侧正面,设有50mm的坡度,以利于焦炉炉顶排水。
(13)焦炉设置DCS控制系统,提高了焦炉操作的自控水平及热效率,降低了能耗。
2. 焦化一厂冷鼓工段生产工艺流程概述
来自焦炉的荒煤气,在焦炉桥管处采用75℃左右的循环氨水喷洒冷却后,温度由700-800℃降至80℃左右。经焦炉集气管来的粗煤气和冷凝液(主要为焦油和氨水)通过荒煤气总管进入气液分离器,煤气与冷凝液在此分离。
分离出的粗煤气并联进入横管式初冷器。初冷器分上、下两段,上段用循环水与煤气换热,煤气由约80℃冷却到45℃左右,循环水由≤32℃升高至约40℃;然后煤气进入初冷器下段与制冷水换热,煤气被冷却到21-23℃,制冷水由≤18℃升高到约25℃。冷却后的煤气进入电捕焦油器,利用高压静电场的作用捕集煤气中夹带的焦油雾滴和萘,经电捕后的煤气进入离心鼓风机加压,送往硫铵工段。
初冷器的煤气冷凝液分别由初冷器上段和下段流出,分别经初冷器水封槽后进入上、下段冷凝液循环,分别由上段冷凝液循环泵和下段冷凝循环泵加压后送至初冷器上、下段喷淋,如此循环使用,上段冷凝液循环槽多余的冷凝液溢流至下段冷凝液循环槽,再由下段冷凝液循环泵抽送至机械化氨水澄清槽。
从气液分离器分离的冷凝液及来自冷鼓工段的其它煤气冷凝液全部汇集到机械化氨水澄清槽,利用焦油、氨水与焦油渣的不同比重,澄清后分离成三层,上层为氨水,中层为焦油,下层为焦油渣。分离后的氨水流至循环氨水槽,然后用循环氨水泵抽送至焦炉喷洒冷却荒煤气用;当集气管需要清扫时,用高压氨水泵抽送一部分氨水送集气管清扫使用;当初冷器上段、电捕焦油器、终冷器需要冲洗时,从循环氨水泵后抽送一部分氨水供喷淋清洗使用;多余的氨水由循环氨水泵送至剩余氨水槽,静置分离少量焦油后用剩余氨水泵送至硫铵工段蒸氨塔进行蒸氨。
从机械化氨水澄清槽分离后的焦油由液位调节器流入焦油中间槽,进一步加热脱水后用焦油泵送到焦油脱水槽内,继续静置脱水;焦油中间槽、焦油脱水槽分离出的氨水和少量焦油流入废液收集槽,定期用液下泵送回机械化氨水澄清槽;焦油脱水槽内的焦油静置脱水至水分≤4%后,用焦油泵送往综合罐区焦油贮槽贮存外售。
机械化氨水澄清槽沉到最底部的焦油渣由链式刮板机刮出,收集后定期送往煤场掺煤炼焦。
系统蒸汽冷凝液均通过蒸汽冷凝管汇集至脱硫凝结水槽,定期用凝结水泵送回锅炉房软化水池。
鼓风机系统煤气冷凝液排入鼓风机水封槽,并由鼓风机水封槽液下泵送至机械化氨水澄清槽。
电捕焦油器捕集下来的焦油排入电捕水封槽,冲洗沉淀后的循环氨水也进入电捕水封槽,并由电捕水封槽液下泵一并送至机械化氨水澄清槽。
各贮槽的尾气集中后,由排气风机抽送至排气洗净塔,用循环水循环洗涤后排放。吸收了尾气的循环洗涤废水,由排气洗净泵送往生化废水处理系统进行处理。
工段内各设备及管道排净管排出的废液均排入废液收集槽,定期用废液收集槽液下泵送回机械化氨水澄清槽重新澄清分离。
3. 焦化一厂硫铵工段生产工艺流程概述
由冷鼓工段送来的剩余氨水经原料氨水过滤器后与液碱混合,然后进入氨水换热器与从蒸氨塔底来的蒸氨废水换热,剩余氨水被加热后进入蒸氨塔,在蒸氨塔中被塔底再沸器产生的汽水混合物间接汽提蒸馏,蒸出的氨汽入氨分缩器,用循环水冷却,冷凝下来的液体入蒸氨塔顶作回流,未冷凝的氨汽送至饱和器前主管,与煤气混合后进入饱和器被母液吸收生产硫酸铵。塔底排出的蒸氨废水在氨水换热器中与剩余氨水换热后,温度降至约78℃进入废水槽,然后由蒸氨废水泵送入废水冷却器,用循环水冷却后送至生化处理。蒸氨塔底定期排出焦油进入焦油桶,人工清理外运。外购来的NaOH碱液送入综合罐区,用碱液输送泵送入碱液贮槽,然后由碱液计量泵连续送入进蒸氨塔的剩余氨水管道与剩余氨水混合。
由冷鼓工段送来的煤气经煤气预热器加热后,进入喷淋式饱和器的上段喷淋室,在此煤气分成两股沿饱和器内壁与内除酸器外壁的环形空间流动,经循环母液逆向喷洒并与母液充分接触,煤气中的氨被吸收后煤气合并成一股,沿切线方向进入饱和器内除酸器,分离煤气中夹带的酸雾后,被送往粗苯工段。
在饱和器下段结晶室上部的母液,用大母液泵连续抽出送至上段喷淋室进行喷洒,吸收煤气中的氨,并循环搅动母液以改善硫铵结晶过程。
饱和器在生产时母液中不断有硫铵结晶产生,由上段喷淋室的降液管流至下段结晶室的底部,用结晶泵将其连同一部分母液送至结晶槽沉降,然后排放至离心机内进行离心分离,滤除母液中的结晶,并用热水洗涤。离心机分离出的母液连同结晶槽满流出来的母液自流回饱和器下段的结晶室。
从饱和器满流口满流出的母液,通过插入液封内的满流管流入满流槽,再经满流槽至母液槽,母液槽内贮存的母液用小母液泵送至饱和器顶部作为补充母液和二次喷洒之用。
外购浓硫酸卸至硫酸贮槽,再用硫酸泵送至硫酸高位槽,然后经流量控制自流入满流槽内。饱和器定期补水,并用水冲洗饱和器,所形成的大量母液由满流槽流至母液贮槽。
带入母液中的焦油,在饱和器下段结晶室上部由焦油排出口排至满流槽,满流至母液贮槽,定期捞出。
当硫酸高位槽的液位高时,可满流至硫酸贮槽,再定期用泵送回高位槽使用。
从离心机卸出的硫铵产品,由螺旋输送机送至干燥器,用被热风机加热的空气干燥,然后称量、包装,送入成品库。干燥冷却器顶部排出的尾气,经旋风分离,由引风机引出,再经过水浴器过滤洗涤尾气中夹带的硫铵颗粒,后排至大气。
4. 焦化一厂洗脱苯工段生产工艺流程概述
来自硫铵工段的煤气首先进入终冷塔冷却,经终冷塔上段的循环水和下段的制冷水换热后,煤气由55℃左右降至25~27℃,然后由洗苯塔底部入塔,自下而上与塔顶喷淋的循环洗油逆流接触,煤气中的苯被循环洗油吸收,洗涤后煤气送入脱硫工段。
洗苯使用的贫油,由贫油槽用泵送往贫油冷却器分别被循环水和制冷水冷却至约30℃,送洗苯塔喷淋洗涤煤气。洗苯后的富油用泵加压去脱苯系统将所含的苯和萘脱除回收,脱除了苯和萘的热贫油自流入油油换热器与富油换热,使其温度降至90℃左右进入贫油槽,并由贫油泵加压送至一段贫油冷却器和二段贫油冷却器,分别被循环水和制冷水冷却至30℃左右,送洗苯塔循环喷淋洗涤煤气。
洗苯塔底富油首先经富油泵加压后送至粗苯冷凝冷却器,与脱苯塔顶出来的粗苯蒸汽换热,将富油预热至60℃左右,然后进入油油换热器,与脱苯塔底出来的热贫油换热,富油在此被160~190℃的热贫油加热到130~150℃后进入管式炉,在管式炉中富油被加热到180℃~190℃后进入脱苯塔。在塔中蒸出的粗苯、蒸汽从塔顶逸出进入粗苯冷凝冷却器被冷却,粗苯、蒸汽被冷凝成液体后进入油水分离器进行分离,分离的粗苯进入粗苯回流槽,部分粗苯经粗苯回流泵送至脱苯塔顶作回流,其余部分溢流入粗苯贮槽,然后由粗苯输送泵送往罐区贮存。由粗苯油水分离器分离的油水混合物入控制分离器,在此分离出的洗油去地下放空槽,然后用液下泵送入贫油槽。分离出的水满流至冷凝液槽,与终冷冷凝液一并送冷鼓工段机械化氨水澄清槽循环使用。
在洗脱苯的操作过程中,循环洗油的质量逐渐恶化,为保证洗油质量采用洗油再生器将部分洗油再生。洗油再生量为循环洗油量的1~1.5%,用过热蒸汽加热,蒸出的油汽进入脱苯塔,残渣排入残油池定期送往煤场配煤或外销。
蒸汽被粗苯管式炉加热至400℃左右,作为洗油再生器和脱苯塔的热源。
外购的新洗油卸入罐区新洗油地下槽,用新洗油液下泵送入新洗油槽,由贫油泵补入系统中。
煤气经终冷塔冷凝所得的冷凝液进入冷凝液水封槽,然后溢流至冷凝液贮槽,由冷凝液输送泵送往终冷塔下段循环喷淋,多余部分送机械化氨水澄清槽,终冷塔上段用冷鼓来的氨水定期喷淋。
5. 焦化一厂脱硫工段生产工艺流程概述
由洗苯工段送来的焦炉煤气,含H2S量约6g/ Nm3,压力为2.5~12KPa,温度约25-28℃,首先进入除油器,脱除煤气中的少量洗油雾后,进入1#脱硫综合塔的脱硫段,在脱硫段下部先经过喷淋洗涤层,再进入上部填料层与脱硫母液逆向充分接触,煤气中硫化氢、氰化氢等酸性气体被碱性母液吸收,并生成相应盐类,煤气在净化吸收过程也被温度高的脱硫母液加热到30℃左右,煤气至塔顶经除雾层除雾后从塔顶排出,又进入2#脱硫综合塔的脱硫段,经洗涤层、填料层与脱硫母液充分接触,煤气中硫化氢、氰化氢被脱硫母液进一步净化吸收,经塔顶捕雾层除雾后排出塔外,送往气柜、焦炉地下室等后续工艺系统。
1#、2#母液循环槽的贫母液由母液循环泵分别加压后,分别送入1#、2#脱硫综合塔,每个塔分两股;一股送入脱硫综合塔顶部向填料层喷洒,另外一股进入填料层下部喷洒。
脱硫母液在综合塔上部脱硫段吸收硫化氢后成为富液,富液从脱硫段下部通过中央液封自流至综合塔反应段,反应段的富母液靠液位自流至其下部的低压双射流再生器的液体分配室,并以射流方式进入混合室,与再生空气射流乳化混合,母液中HS-在催化剂作用下被氧氧化成单质硫,气、液、固三相流体由低压双射流再生器排出管排至再生浮选段下部,转向上流,氧化反应继续进行,空气泡对单质硫产生浮选作用,气、液、固三相混合物在再生浮选段流动过程完成分离任务,尾气脱离液面,由再生段顶部侧面排出塔外,硫磺泡沫漂浮于溶液表面,通过周边溢流堰进入环形收集槽,由排出口自流至硫泡沫槽;与气固分离后的贫母液进入贫液收集槽,经1#、2#脱硫综合塔的液位调节器分别自流至1#、2#母液循环槽。
为控制硫泡沫中母液含量,必须严格控制通过溢流堰硫泡沫液体的总量,通过塔外液位调节器可以有效调节再生段内硫泡沫层的液面高度,从而控制硫泡沫排出总量。
再生空气由1#、2#再生风机分别提压后,分别送至两综合塔再生段的空气管,使压力达到25-30KPa之后,送至每个低压双射流再生器的空气分配室,并以射流形式进入气液混合室,使脱硫循环液得以再生。
硫泡沫在硫泡沫槽内搅拌后,经泡沫泵送至脱硫离心机进行离心脱水,产生的硫膏进入硫膏接收槽,然后通过硫膏输送泵压入熔硫釜内进行熔硫,生成硫磺外售。清液则流入溶液缓冲槽,一部分回流至母液循环槽循环使用,一部分则直接排至地下槽,通过液下泵输送到煤塔进行喷洒。
脱硫蒸汽冷凝液槽满槽后,联系锅炉房,将蒸汽冷凝液用泵输送至锅炉房。
6. 焦化一厂储配工段工艺流程
脱硫后的煤气进入气柜,加压机将气柜中的煤气输送至古交等区域供城市用气。
7. 焦化二厂
焦化二厂选用山西化工设计院QRD—2000清洁型热回收捣固式焦炉。该焦炉设计规模为8×16孔,年焦炭生产能力为60万吨/年。
该焦炉的主要特点:利用炼焦烟气燃烧,在炉顶、两侧炉墙和四联拱底加热火道加热碳化室,炼焦生产的焦炉煤气和各种物质在炉内烧尽,炉内负压操作,可消除常规机械焦炉产生的氨、萘、硫等有害副产品,同时可为炼焦过程提供直接热源。炼焦采用预捣固快速侧装煤,平接焦工艺,可提高焦炭质量,减少出焦粉尘,保护环境。
备煤车间将炼焦所需煤种通过受煤坑,由皮带机送至配煤仓。配煤仓下设称重式给料电子皮带秤进行配煤,计算机控制。按照一定比例将配合煤送至破碎机,进行煤炭的破碎。破碎细度达到工艺要求后再经皮带机分别送到焦炉煤塔供炼焦车间使用。
炼焦车间的设置布置:8×16孔QRD—2000清洁型热回收捣固式焦炉双排布置,在两32孔中间放有焦炉煤塔,煤塔储量1100t,煤塔下设有捣固站,内设有移动式布煤小车,单排6锤捣固机两套,一备一开。在煤塔两旁设有炉门及焦炉机械修理站各一座。
两排焦炉设有两个高为75m的烟囱,布置在焦炉机侧,在焦炉另一端设有一套湿法熄焦系统,熄焦塔上设有挡板除尘装置,有利于保护环境。
筛焦工段负责将炼焦工段熄灭的焦炭卸至晾焦台、经放焦至皮带运输机,至滚筛进行分级,目前焦炭分级为0-25/25-90/90-130/130以上的四个级别。
发电车间是西山煤气化公司焦化二厂QRD——2000清洁型热回收捣固式机焦项目的一个重要配套工程。该车间的建设,可使焦炉生产中的高温烟气得到充分利用,同时对排入大气环境终端的烟气进行脱硫除尘,达标排放,符合国家发展循环经济、提高能源综合利用的政策;符合清洁发展机制(CDM)、实现节能减排;符合环保政策、实现可持续发展;对建设环境友好型、资源节约型社会具有较大的现实意义。
本发电工程采用四台Q90/950——35——450/3.9型余热锅炉,回收焦炉高温烟气中的热量,生产出中温中压蒸汽,通过蒸汽母管送至发电主厂房。
主厂房两台KN15——3.43——2型空冷凝汽式汽轮机利用中温中压蒸汽分别带动两台QF——K15——2型发电机进行发电。发电机发出的10.5KV电能通过升压变,将电压升至110KV后并入电网。
在余热锅炉内部进行了热交换后的焦炉烟气,通过四台Y4——73N018D型离心式引风机的吸力和烟道的吸力作用,分别经过四台XDT——35型脱硫除尘塔和引风机后从两座70米高烟囱排入大气。烟气在经过脱硫除尘塔时,被双碱法湿式除尘工艺除去了烟尘、SO2等有害气体,达到环保排放要求后排放。
在凝汽式汽轮机中做功后的乏汽,通过输汽管道进入空冷系统。乏汽经过空冷凝汽器后变成凝结水,凝结水精处理后循环使用。
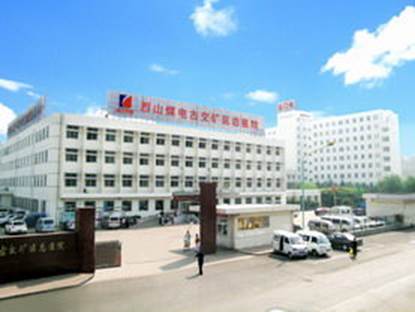
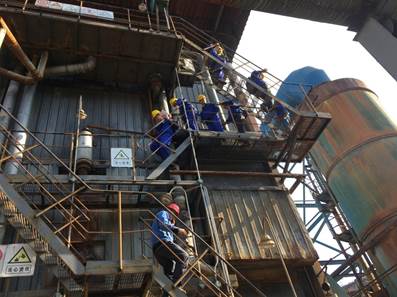
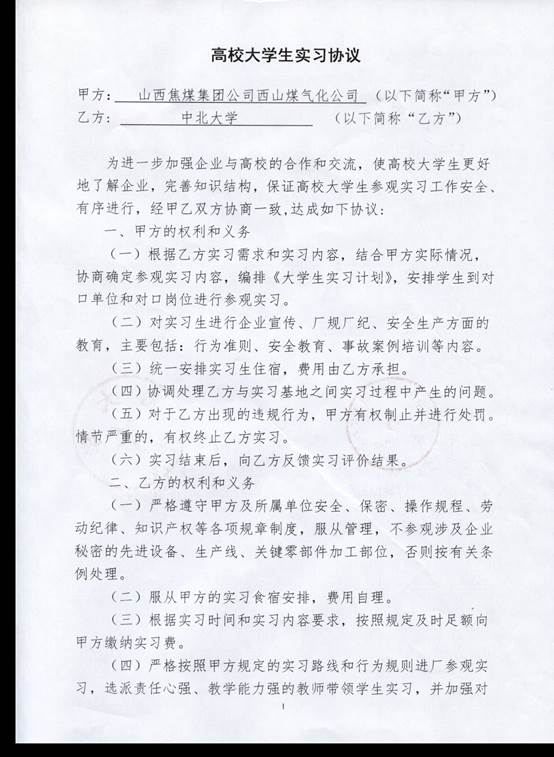
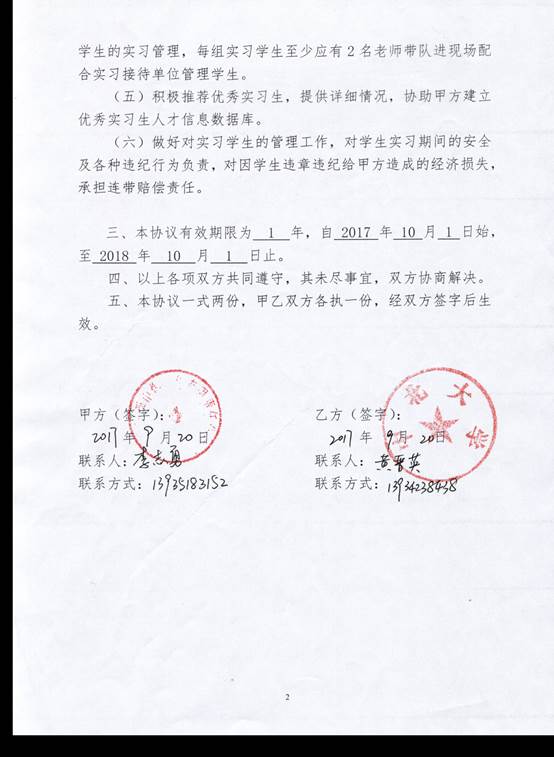